6-Axis Deep-Hole Drilling & Milling Center in Mold Manufacturing:Applications & Advantages
- 邵萱 黃
- Jul 9
- 3 min read
Updated: 3 days ago

Deep hole drilling is a high-precision machining technique specifically developed for creating holes with significant depth. It offers excellent control over hole diameter, depth, and internal surface finish, and is widely used in mold manufacturing involving materials such as steel, stainless steel, and aluminum alloys.
Mold Applications of
6-Axis Deep-Hole Drilling & Milling Center
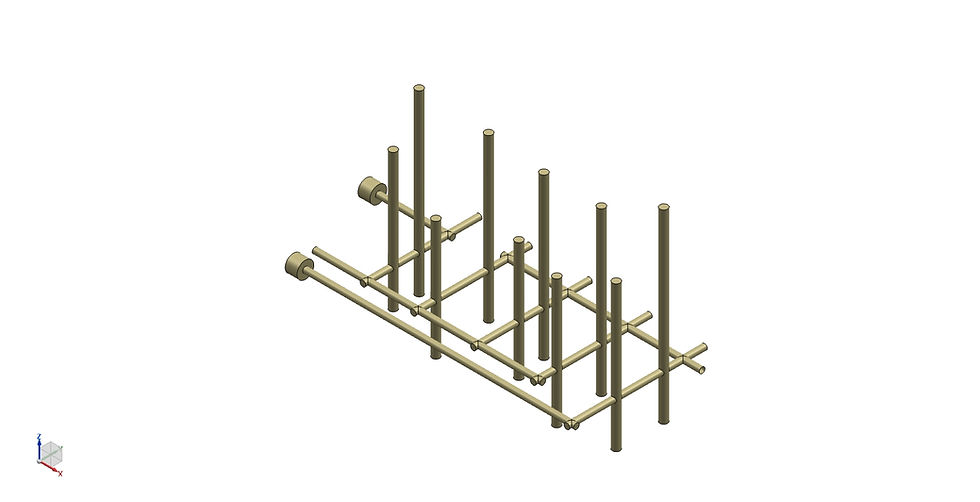
1. Cooling Channel Machining
Temperature control during mold processing has a direct impact on the final product quality, making cooling channel design a critical aspect of mold manufacturing.
Using deep-hole gun drilling, cooling circuits can be machined with high precision, significantly improving thermal efficiency, shortening production cycles, and reducing product warpage and scrap rates.
In automotive lighting plastic molds, accurate and well-planned cooling channel layouts are essential to ensure dimensional stability and consistent optical performance.

2. Ejector Pin Hole Machining
Ejector pin holes are typically long and narrow, making them prone to misalignment and rough internal surfaces when using conventional drilling methods.
By applying deep-hole gun drilling technology, it is possible to ensure excellent straightness and perpendicularity of the holes, which enhances the smoothness and reliability of the ejection process. This ultimately improves the surface quality and dimensional accuracy of the molded parts.
3. Enhancing Mold Precision and Service Life
Deep-hole gun drilling helps to minimize residual stress within the mold, preventing deformation and cumulative dimensional errors during machining. This significantly enhances both the service life of the mold and the stability of the molded product.
The technique is particularly suitable for industries with extremely high precision requirements, such as the automotive sector, where it plays a critical role in the manufacturing of automotive lighting molds, ensuring optical consistency and precision alignment.
HOWMIN’s Equipment Advantages
HOWMIN has introduced an advanced multi-functional deep-hole machining system featuring multi-axis control, a high-rigidity machine bed, a BT-50 milling spindle, and a rotary working table. It is capable of machining hole diameters from Ø3 to Ø30 mm, with a maximum drilling depth of up to 1500 mm.
This all-in-one system integrates both milling and deep drilling capabilities, significantly improving the efficiency and accuracy of machining complex mold structures such as cooling channels and ejector pin holes, while reducing cycle time and cumulative errors.
Advantages Gained After Equipment Upgrades
Simultaneous multi-angle deep-hole and milling operations reduce repositioning and setup time.
Significantly improved hole straightness and surface finish enhance overall product quality.
High machining flexibility supports complex geometries and customized cooling or ejector pin layouts.
These equipment-driven technical advantages not only enhance production efficiency but also strengthen HOWMIN’s market competitiveness in the field of automotive lighting plastic molds.
Why 6-Axis Deep-Hole Drilling & Milling Center Outperforms Conventional Drilling
High-Precision Machining: Enables accurate control of hole diameter and depth, minimizing dimensional errors.
Superior Surface Finish: Reduces the need for secondary surface treatments and lowers overall finishing costs.
Excellent Thermal Performance: Effectively enhances the cooling capacity of the mold.
Wide Range of Applications: Suitable for deep-hole machining of cooling channels, ejector pin holes, guide pin holes, and more.
Cost-Effective: Reduces tool wear and lowers overall machining costs.
Deep-Hole Machining Considerations in the Mold Design Stage
Taking deep-hole machining requirements into account during the mold design stage helps improve downstream machining efficiency and quality. Designers should clearly define the location, dimensions, and orientation of cooling channels and ejector pin holes to avoid complications and increased costs during later manufacturing stages.
Conclusion
Deep-hole gun drilling has become an essential technology in the mold manufacturing industry, thanks to its high precision, efficiency, and cost-effectiveness. By introducing advanced equipment and integrating comprehensive machining capabilities, HOWMIN continuously enhances mold quality and production efficiency—solidifying its competitive edge in the automotive lighting mold market.